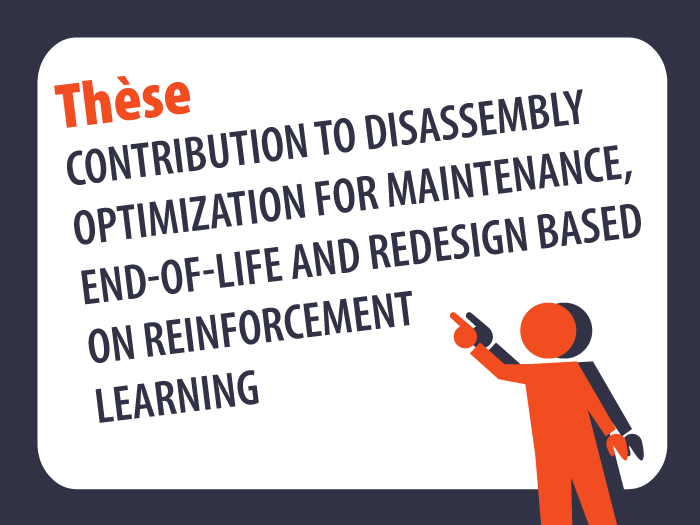
On Friday 1st December 2023, at 9.30 am, Ms Amal Allagui will defend her thesis at ISAE-Supméca entitled Contribution to disassembly optimization for maintenance, end-of-life and redesign based on reinforcement learning, directed by Ms Olivia Pénas (ISAE-Supméca – Quartz) and co-directed by Messrs Nizar Aifaoui (ENIM), Régis Plateaux (ISAE-Supméca – Quartz) and Moncef Hammadi (ISAE-Supméca – Quartz). Nizar Aifaoui (ENIM), Régis Plateaux (ISAE-Supméca – Quartz) and Moncef Hammadi (ISAE-Supméca – Quartz).
Keywords
# Computer-aided design
# Reinforcement learning
# Optimization of disassembly sequences
# Preventive maintenance
# End-of-life disassembly, MBSE
Abstract
The process of disassembling mechanical parts represents a crucial stage in the product life cycle, and is recognized as a major economic challenge at industrial level. Furthermore, one of the major challenges is the automatic generation of optimized mechanism disassembly sequences. The subject of this thesis addresses the optimization of the disassembly sequence planning process in a maintenance or end-of-life context, and the consequent redesign of mechanical assemblies. The aim is to provide decision support in the maintenance and/or disassembly phase at end-of-life. Furthermore, underlining the importance of the time factor in the manufacturing industry and its high contribution to product production costs, this thesis aims to find a tool capable of providing an optimal disassembly sequence guaranteeing the minimum implementation time, while also minimizing the generation time of this sequence. The disassembly sequence optimization parameters considered are as follows: minimizing change of direction during disassembly operations, minimizing tool change, facilitating access to wear parts during disassembly for maintenance purposes, and favoring disassembly of small parts first. These results were used to propose alternative ways of redesigning CAD architectures for mechanical assemblies in order to optimize disassembly sequences. Following a needs analysis conducted using an MBSE approach, an in-depth state-of-the-art review was carried out to examine the work carried out in this field. Through this review, we were able to identify the research goals that guided our thesis objectives. To implement these approaches, we developed a software tool, using data from the CAD environment and a Python platform. We validated the effectiveness of this tool by applying it to several examples and comparing it with works from the literature.